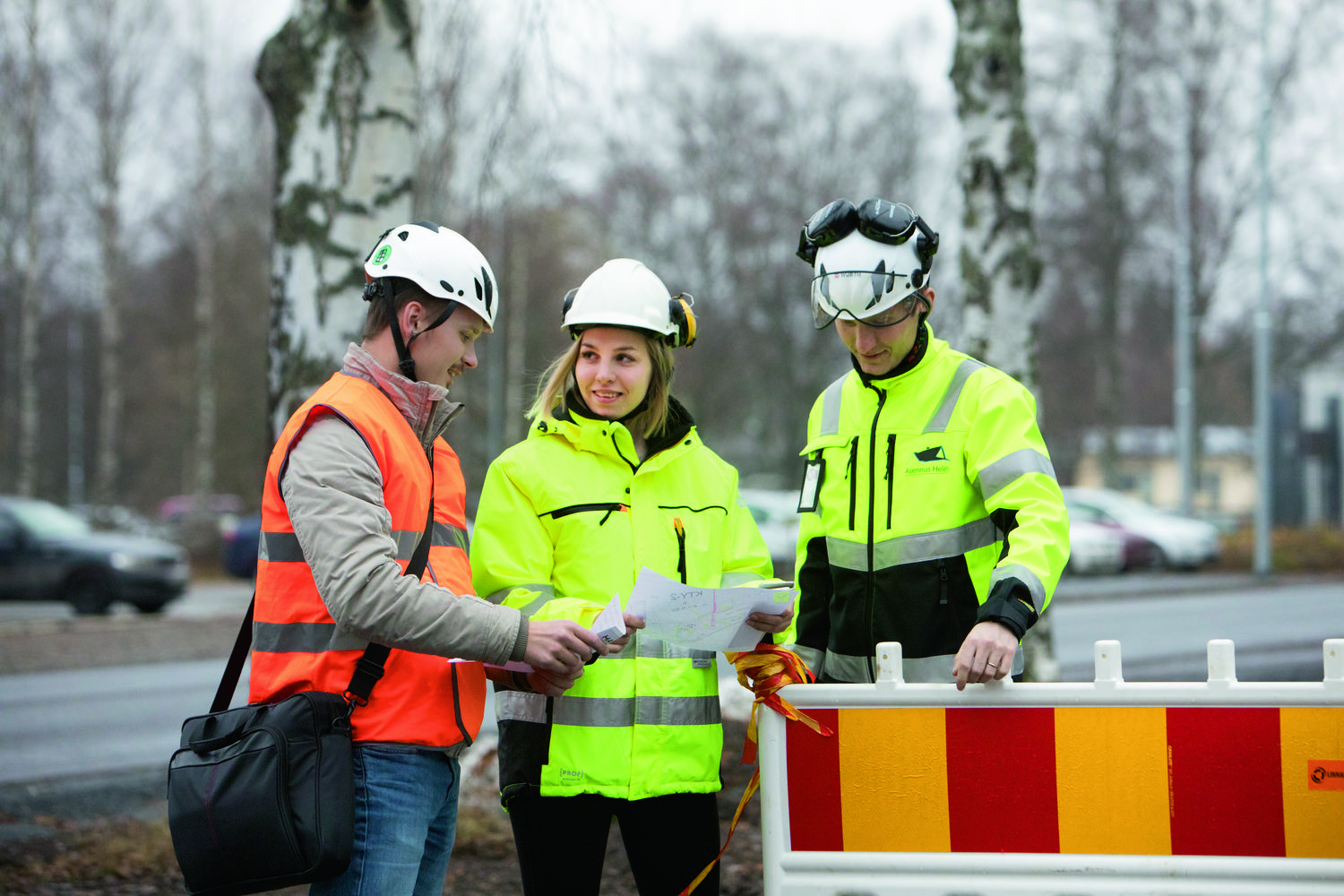
DreamFAB
Deconstruction and refabrication for the reuse of steel buildings
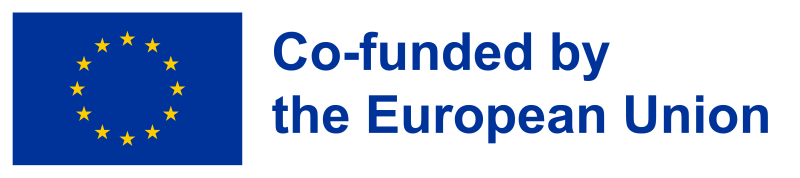
Project info
Project | Deconstruction and Refabrication for the Reuse of Steel Buildings (DreamFAB) |
Duration | 1.9.2023 – 31.8.2027 |
Implementors | Häme University of Applied Sciences, University of Coimbra, Polytechnic University of Timisoara, FERPINTA Group, ROBOPLAN, Wurth Oy, Jupa S. A., SSAB Europe Oy, STAR Institute |
Funding | European Research Fund for Coal and Steel (RFCS) |
Budget | 2 500 000 € |
Deconstruction and Refabrication for the Reuse of Steel Buildings (DreamFAB) -project will develop and validate the technical rules and re-fabrication guidelines for the structural safety of reuse and re-fabrication of steel buildings and develop solutions for composite beams, roof trusses and robot-assisted deconstruction.
At the end of building life, more than 95 % of the steel used is recycled and new steel is made from it. Steel recycling – melting and solidifying it again – is an energy intensive process, but reusing the steel elements instead of producing new steel could save 96 % on the environmental impact. So far, the recyclability of steel is still a priority at 93 % of the steel being recycled, and the reuse of steel sections is estimated at only 6 %.
Deconstruction and Refabrication for the Reuse of Steel Buildings (DreamFAB) -project will develop and validate the technical rules and re-fabrication guidelines for the structural safety of reuse and re-fabrication of steel buildings, develop the innovative demountable solutions for composite beams and roof trusses using Rectangular Hollow Sections, and develop the solutions for robot-assisted deconstruction. The essential technical rules and solutions will be developed so that the steel elements of buildings can be conveniently re-fabricated and reused without the need of energy-intensive recycling processes. In particular, the project aims to overcome the most critical technical barriers which prevent the reuse of steel constructions.
The benefits of this project to the society include for example more employment opportunities due to deconstruction and re-fabrications instead of demolition and significant energy savings. The whole process becomes faster, safer, and better by the incorporation of robots in the construction and deconstruction of the buildings. The faster production cycle and reuse of structures also has the potential of bringing competitive solutions for the steel construction market. The environmental benefits due to multiple reuses instead of recycling will increase the competitiveness of steel material in the building industry, and hence increase the use of steel.
There are 9 project partners in the DreamFAB-project: Häme University of Applied Sciences (HAMK, the coordinator), University of Coimbra (Portugal), Polytechnic University of Timisoara (Romania), FERPINTA Group (Portugal), ROBOPLAN (Portugal), Wurth Oy (Finland), Jupa S. A. (Spain), SSAB Europe Oy (Finland) and STAR Institute (Portugal).
Work packages
Project implementation is divided to eight work packages.
This work package includes project management and dissemination of the results.
WP2 will analyze the available deconstruction options for composite construction and tubular truss, design the reference buildings: one for a single storey steel-framed building, another for a multi-storey composite steel-framed building.
WP3 will investigate the effects of increased geometrical imperfections due to deconstruction, loading during first life period and refabrications.
WP4 will investigate the effect of multiple welding-cutting-welding thermal cycles and develop the guidelines for structural safety.
WP5 develops and verifies the innovative demountable solutions for composite construction with robot-assisted deconstruction in mind. Both push-out tests and full-scale composite beam tests will be carried out.
WP6 is dedicated to the demountable mechanical solution for tubular roof trusses. The major goal of this work package is to develop and verify the economical demountable non-welded joint solutions for RHS truss application.
WP7 will develop and apply deconstruction robots, to resolve the time constraints and reduce the cost of the deconstruction process. This task aims to propose a new collection of robots designed to operate within the proposed Framework for Robot-Assisted Construction/Deconstruction (FRACD), and demonstrate in the developed test-case scenarios in WP5 and WP6.
The major activities are
• Propose and pre-design a state-of-the-art collection of construction and deconstruction robots based on the proposed FRACD;
• Simulate the construction and deconstruction mechanism, showing the feasibility of the proposed framework and robot models;
• Build a steel-concrete composite construction and demonstrate the deconstruction process;
• Build a tubular roof truss and demonstrate the deconstruction of non-welded roof truss.
WP8 addresses the improvement strategies of design for deconstruction and environmental impact for the buildings by reuse and re-fabrication, to provide quantitative method and tools for reuse design and decision-making. Technical rules and guidelines will be developed in this WP as well.
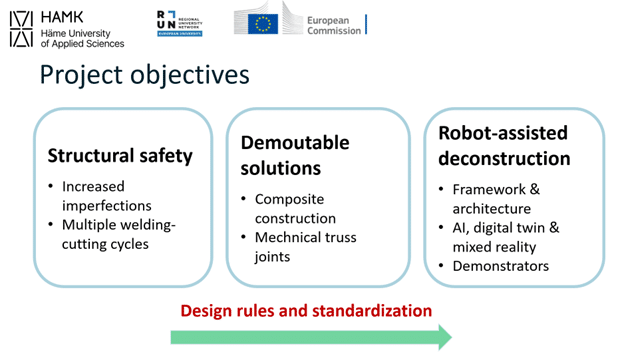
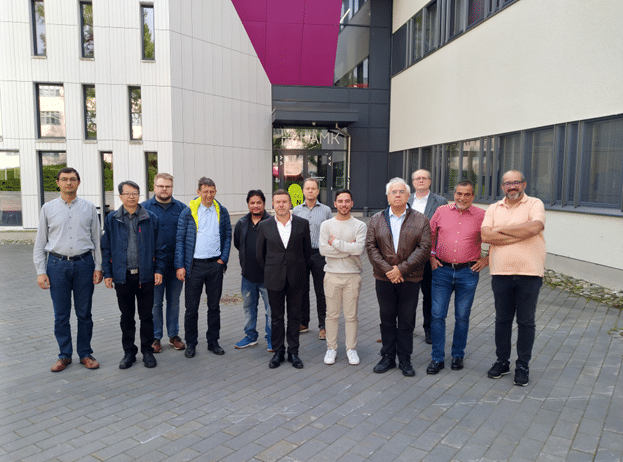
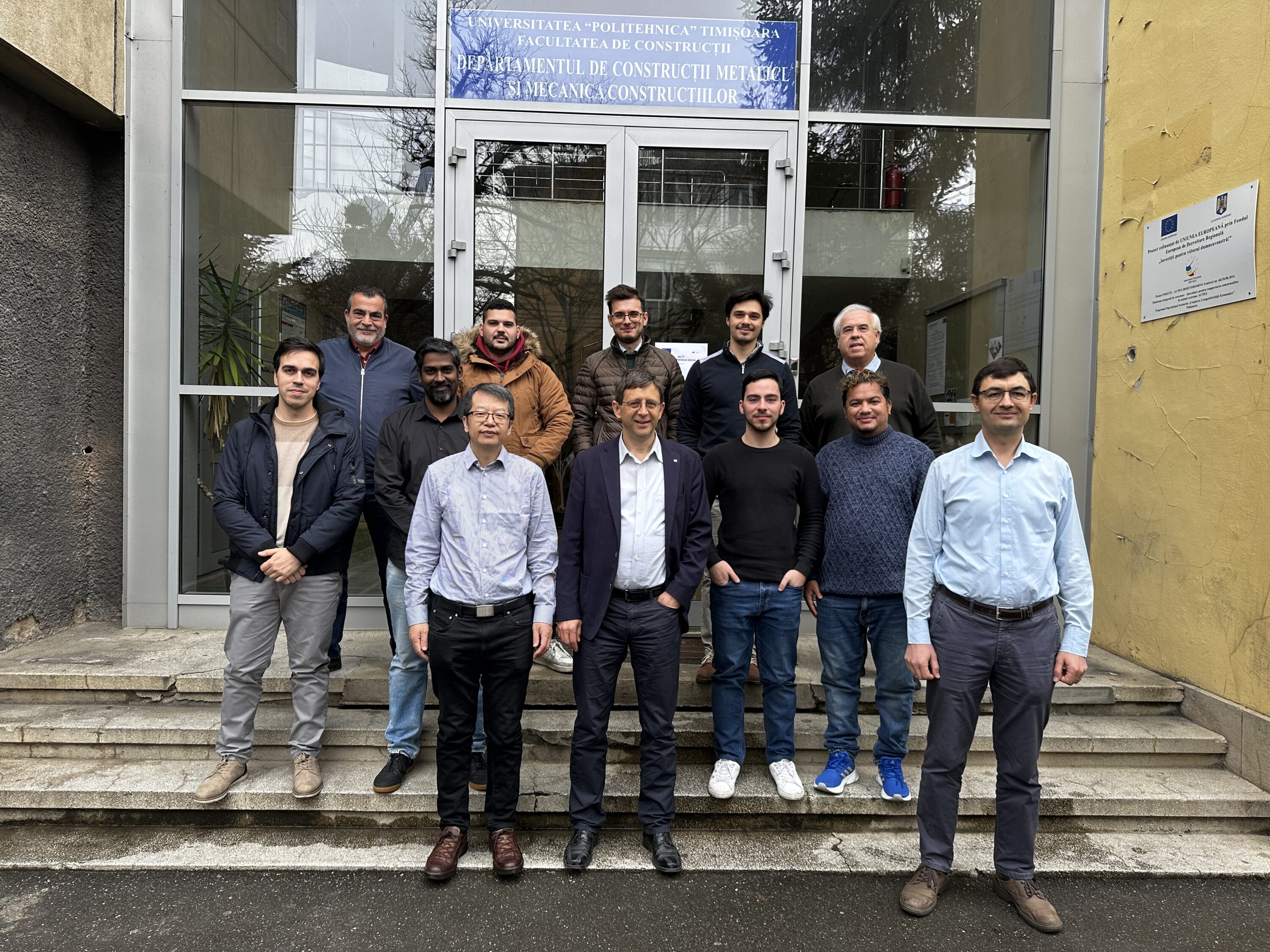
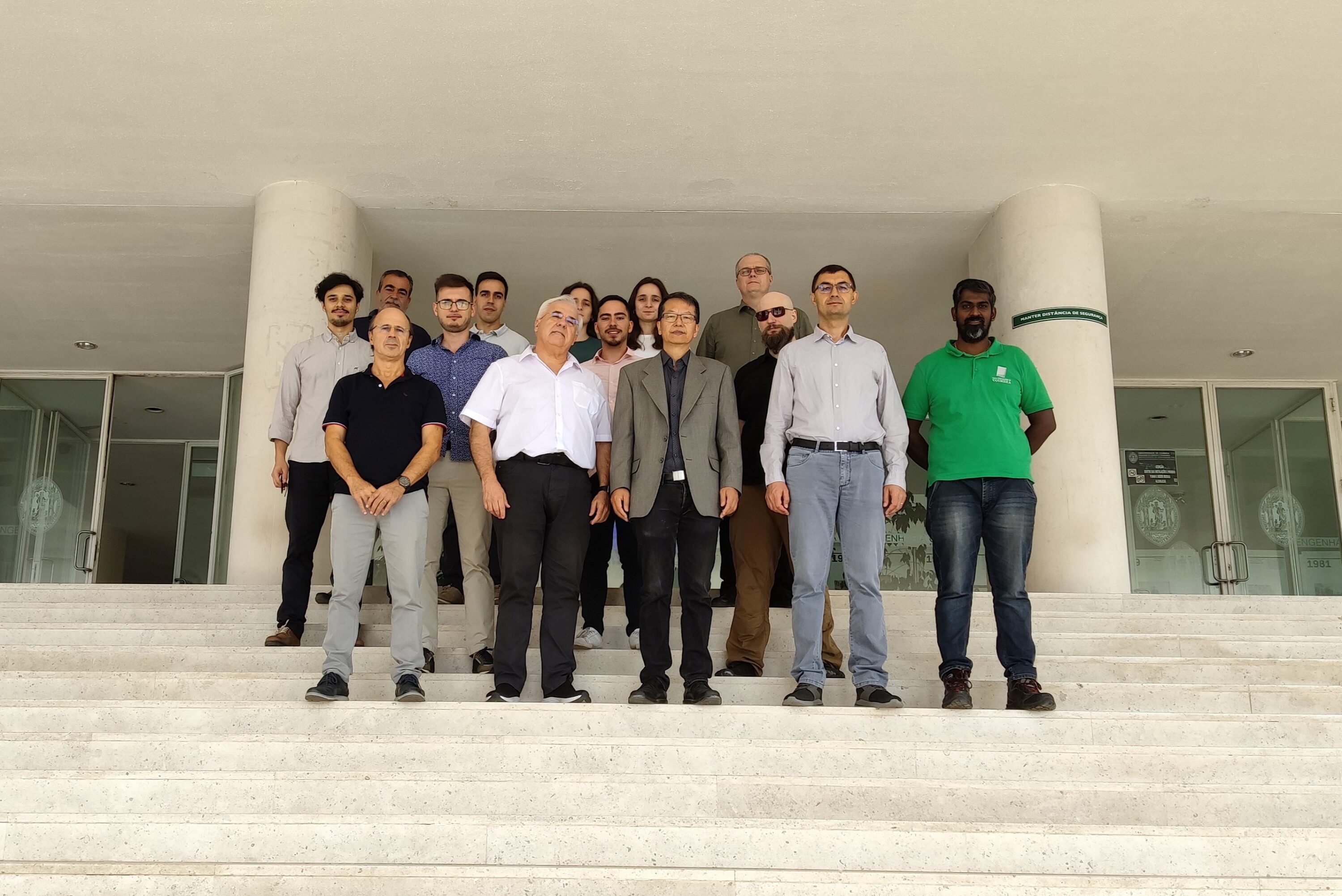
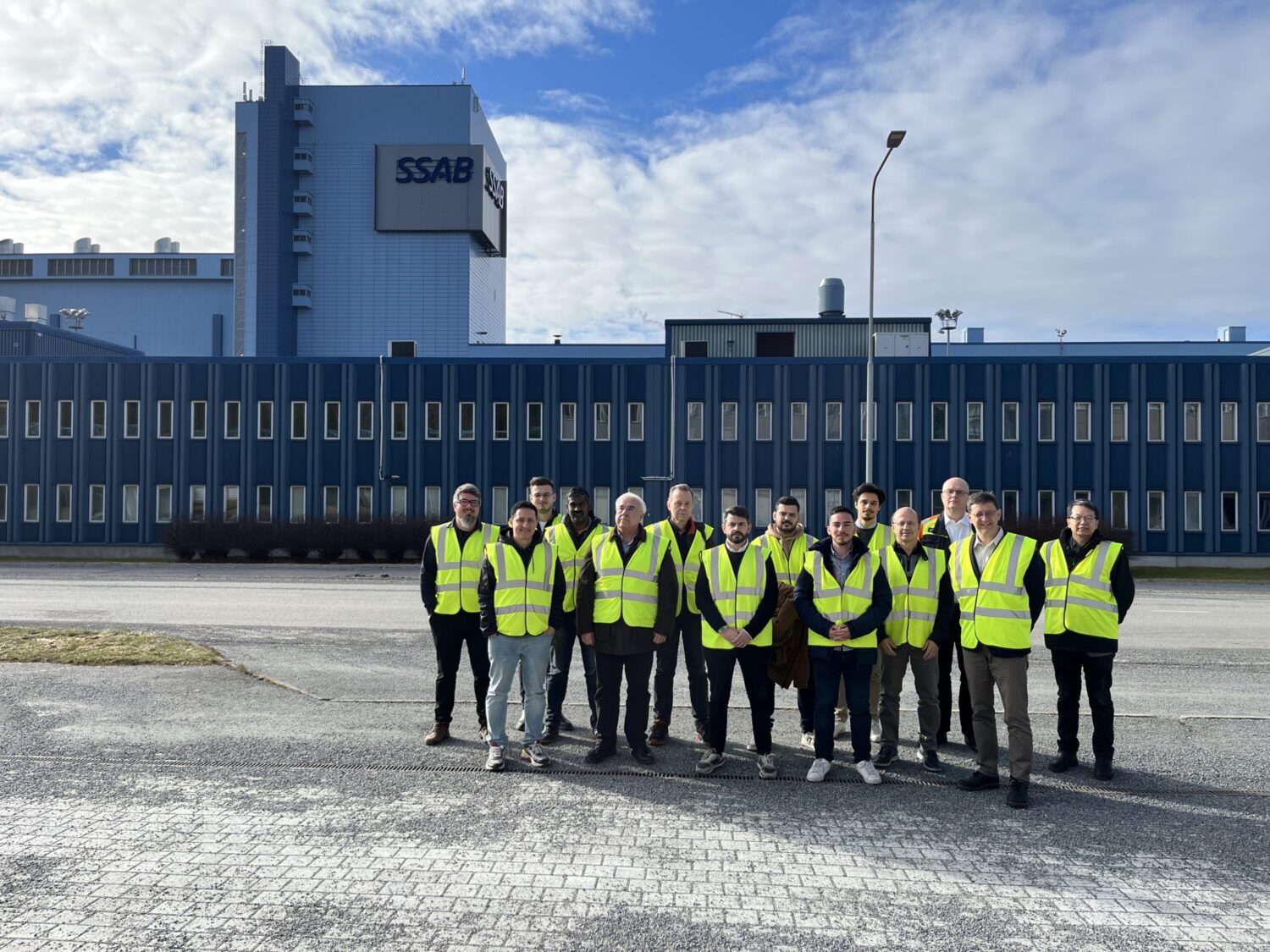
Contact
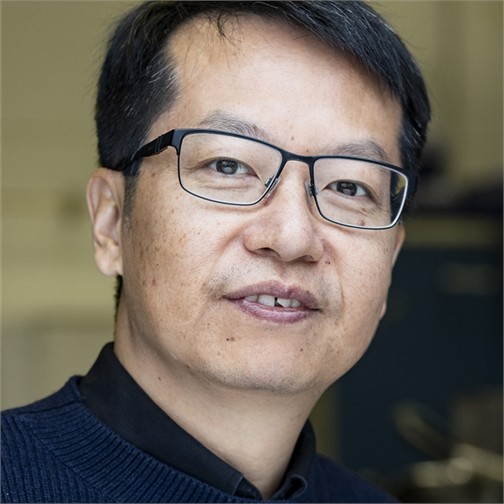
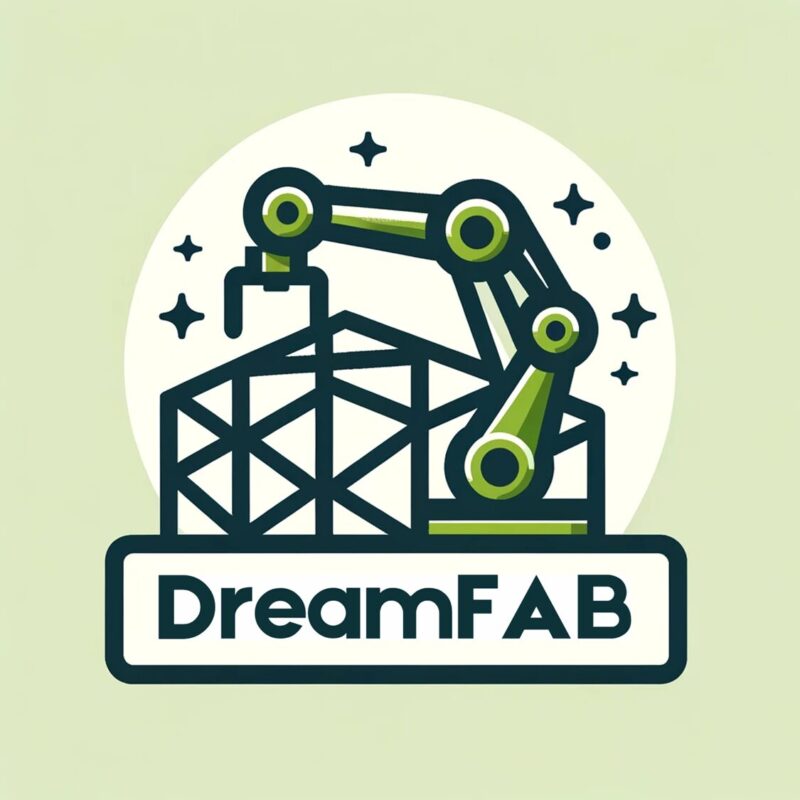
Follow us on social media!
Check out HAMK’s social media channels focusing on research!